Achieving the best performance possible out of your metal parts, especially if the application for those parts is in aerospace, is a challenge for even the most skilled manufacturers. After all, it’s not just cutting and measuring parts, you also need to finish. There is a long list of possible finishing techniques, so choosing the right one and performing it can be tricky. With that in mind, let’s talk about just a few aerospace metal finishing techniques.
Click Here for our The State of Aerospace Manufacturing Infographic
Plating
Metal plating uses a chemical bath to coat or alter the metal’s surface with a thin layer of metal such as cadmium, zinc-nickel, copper, or silver. There are two types of plating: electroplating with generates an electric current to coat the workpiece and electroless plating uses an autocatalytic process. Metal plating provides a number of advantages–it improves durability, corrosion resistance, surface friction, and appearance. It is a fast and efficient solution, but it is not great for smoothing surface defects.
Powder Coating
Like paint, powder coatings are a decorative finish, but with the added benefit of increased durability. The process involves melting dry plastic powders onto the metal to produce either a matte, glossy, or textured coating. This is also an effective method for removing any surface defects.
Metal Vibratory Finishing
Vibratory machines deburr products and remove sharp edges. The material is placed inside a drum filled with pellets and a substrate. Then they are tumbled to achieve a uniform though random finish. The machine’s cycle speed and magnitude of vibration are variable, which allows for effective treatment for a range of part sizes.
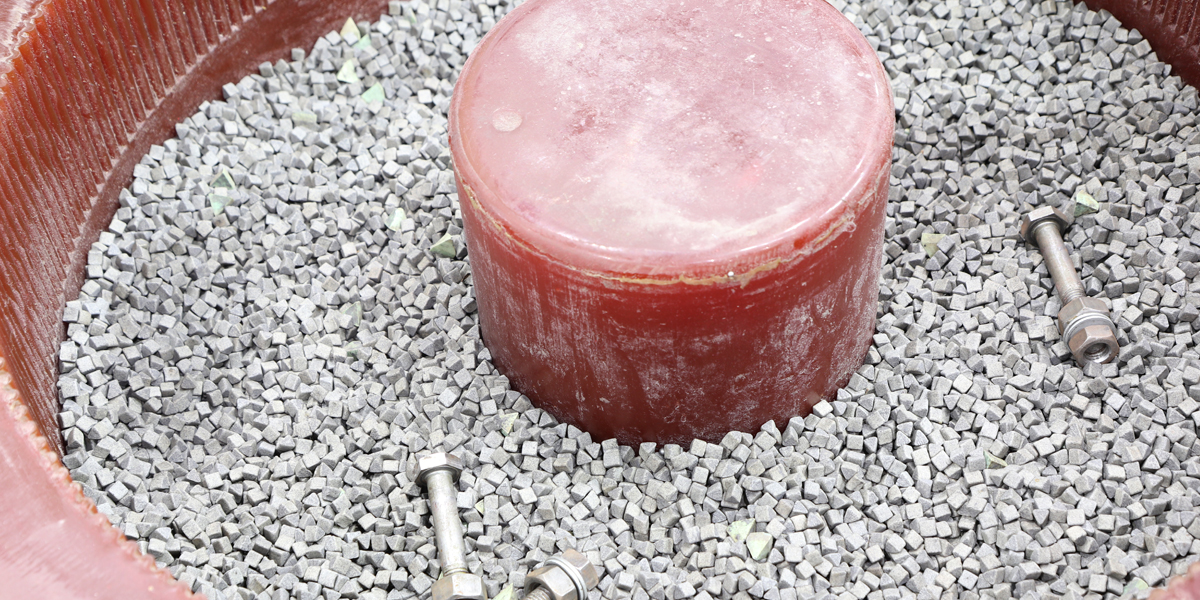
Metal parts being finished in a vibrating drum filled with pellets and a substrate.
Sand Blasting
Sand-blasting machines are typically used in projects requiring a matte finish. The process shoots sand, steel shots, metal pellets, or other abrasives at the substrate. This results in a smooth texture, but it works best for softer metals.
Hot Blackening
Blackening machines spread a thin layer of black oxide onto a substrate’s surface, which creates a matte black finish with high resistance to abrasion. This is a high-temperature process: the product is put into a series of tanks containing cleaners and coolants. This process is mostly used for automotive parts, tools, and firearms.
Grinding
Grinding uses friction, compression, and/or attrition to smooth a metal surface. There are many grinding methods, each with their own applications and processes. Grinding machines are designed to craft different levels of smoothness. Three common types of grinding include centerless grinding, cylindrical grinding, and surface grinding. There is also vertical grinding which pushes traditional horizontal grinding on its side, which is a boon for increasing the grinding wheel’s lifespan.
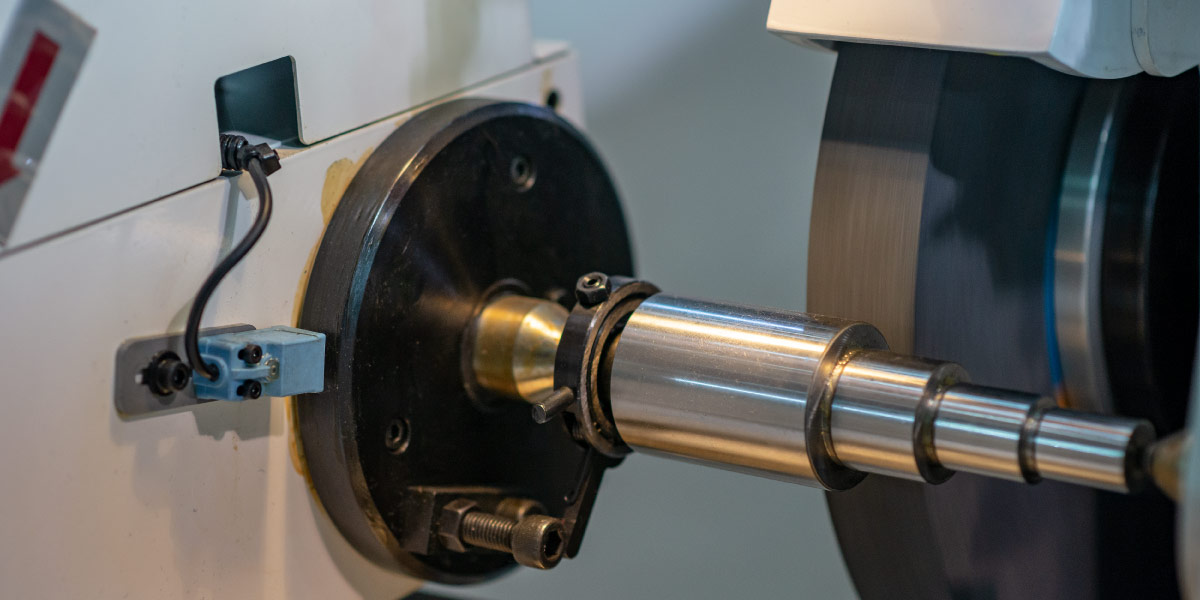
The type of grinding wheel you use is determined by a number of factors, including part material, and desired finish.
HVOF and Thermal Spray Coating
Thermal spray coatings and High Velocity Oxygen Fuel (HVOF) coatings use molten or semi-molten materials projected at high-speeds onto the substrate. These materials are made up of powders which include metals such as aluminum or stainless steel. They are mixed into a chamber, oxygen and some other fuel is added, and the particles are shot out of the nozzle at the substrate to create a coating. These coatings are harder, resist degradation, and take on less residual stress—which resists cracking.
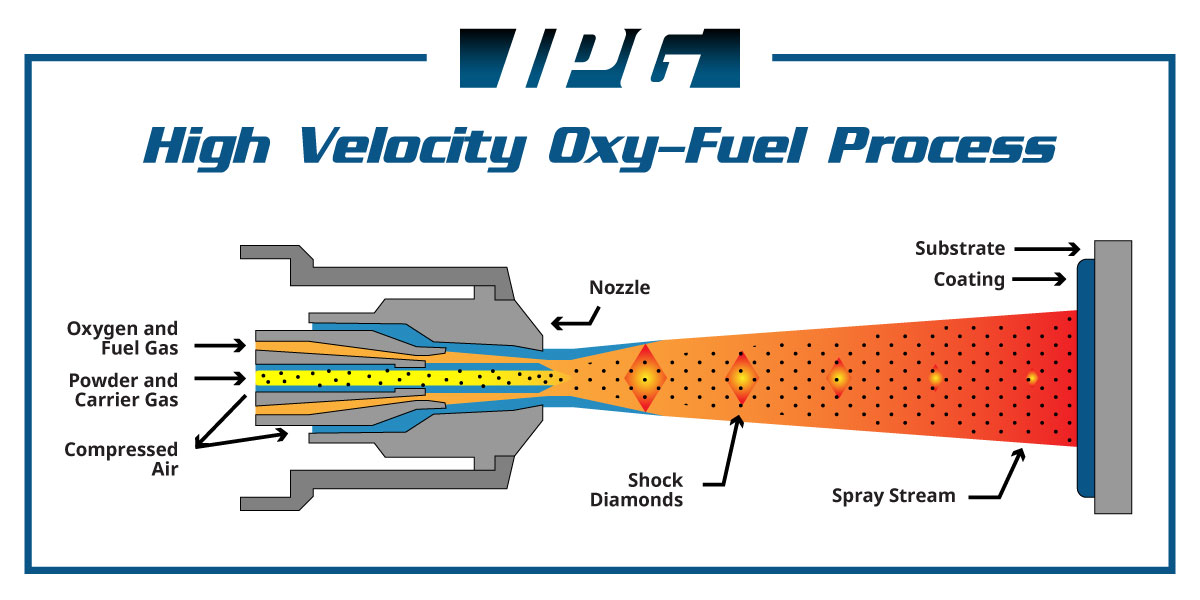
The HVOF process uses the combustion of fuel and oxygen to propel a corrosion-resistant powder at the part being finished.
When we talk about developing metal finishing techniques, we look for tangible or even quantifiable benefits to these techniques. The benefits often seek to target one or more of the following:
- Reduce maintenance
- Reduce the use of toxic chemicals and waste
- Reduce rework cycle times
- Maximize yield
- Provide flexibility
- Reduce life cycle costs
- Increase net profits
Finishing is both art and science, which is why a specific process is needed to achieve the desired finish. Whatever your aerospace metal finishing needs, the team at IPG is equipped to meet them.
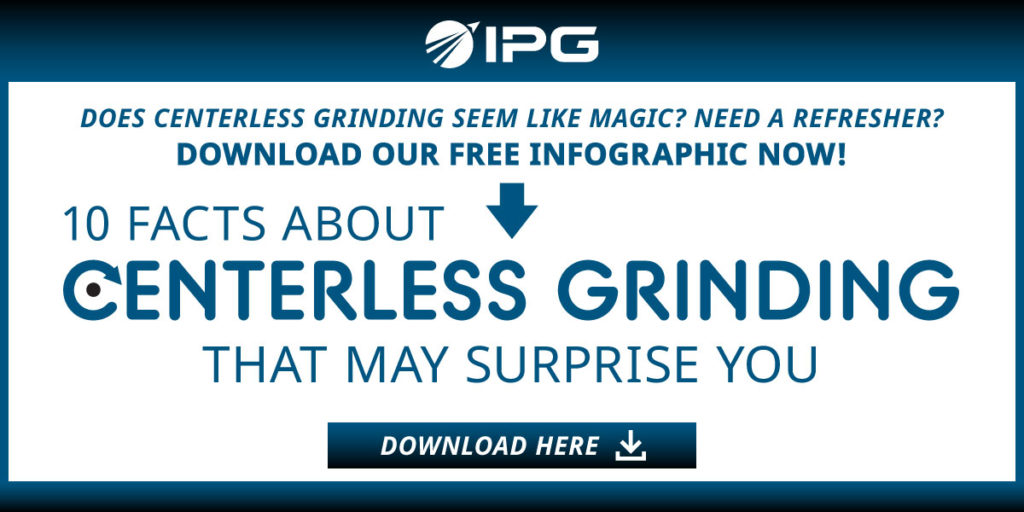